Wausau will be exhibiting at Greenbuild in booth #2820
Wausau Window and Wall Systems’ curtainwall systems with vertical sun shade blades are being installed by R.A. Kennedy and Sons on the University City Science Center’s new mixed-use tower under construction at 3737 Market Street in Philadelphia. The building intends to achieve LEED® Silver certification for environmental and energy efficient design, and is expected to be completed in June 2014.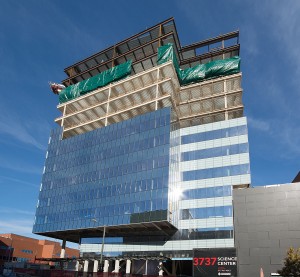
Designed by the internationally renowned architecture firm of Zimmer Gunsul Frasca Architects (ZGF) in cooperation with UJMN Architects + Designers, the building is owned by the Science Center and its joint venture partner, Wexford Science + Technology, LLC. Penn Presbyterian Medical Center will be the anchor tenant in this 14-story facility.
General contractor INTECH Construction broke ground in September 2012 and is on schedule for next summer’s grand opening. The 295,000-square-foot structure will contain outpatient medical facilities, ground-floor retail, and office and laboratory space for start-up and growing companies. It also serves as an integral part of the transit-oriented neighborhood taking shape in the city’s western edge, adjacent to the University of Pennsylvania and Drexel University. Established in 1963, the Science Center was the first, and remains the largest, urban research park in the United States encompassing 17 acres.
Wausau’s curtainwall and sun shade products support the Science Center’s 3737 Market Street project in reaching its on-time completion and in pursuing Silver certification through the U.S. Green Building Council’s LEED Green Building Rating System for New Construction. These products combine the benefits of natural light and outside views with recycled content, low-emitting materials and energy optimization.
Pennsylvania-based glazing contractor R.A. Kennedy and Sons is installing 130,000 square feet of Wausau’s aluminum-framed curtainwall systems. Of this total, the significant majority of the building is enveloped in Wausau’s INvision™ 7250i-UW Series thermal unitized curtainwall. The units typically are off-loaded at the project site using the main construction crane, then erected by stacking individual panels vertically and horizontally, resulting in a four-way-stack-joint design.
R.A. Kennedy and Sons began the curtainwall installation at the second floor, moving upward, and then finishing with the ground floor. “The largest frames are 5-foot-3-inches wide by 22-foot-10-inches tall, weighing roughly 1,500 pounds,” says Al Batten, project manager at R.A. Kennedy and Sons. “These are being installed on the East elevation, which abuts an existing building. This eastern side goes from the fifth floor to the penthouse. At the penthouse mechanical screen area, some of the units are 7-by-18-feet — not as big, but 14 stories in the air.”
“Using INvision unitized curtainwall, handling for each unit is minimized, which decreases the opportunity for a mishap and saves time overall. Installation time is a fraction of that necessary for field-glazed systems,” explains Wausau’s health care market manager, Lisa May, LEED Green Associate.
INvision unitized curtainwall systems’ interlocking frame design accommodates seismic, live load and thermal building movements. For 3737 Market Street, the INvision 7250i-UW curtainwall needed to be engineered with a custom horizontal unit stack at each level, accommodating 1-inch of total vertical movement. For long-term durability, vertical movement — as well as horizontal movement — is taken through gasketed slip joints, not through slippage of glass within glazing pockets or extension or compression of sealant joints. This four-side silicone structural-glazed system features 3-inch mullion sightlines and 6.25-inch frame depths that incorporate polyamide thermal barriers, which contribute to a building’s thermal performance, condensation resistance and energy efficiency.
May adds, “New Model Energy Codes are being adopted by local and state jurisdictions nationwide, demanding improved curtainwall framing thermal performance. When glazed with spectrally selective, low-emissivity insulating glass units and a thermal barrier, INvision systems meet the most stringent of thermal requirements — even in northern climate zones — and help address sustainable design goals for many buildings.”
A combination of Viracon glass types is used to facilitate 3737 Market Street’s daylighting and energy efficiency objectives. In the vision areas, 1-inch, low-emissivity insulating VRE1-46 glass was specified. In the spandrel areas, where the insulating glass conceals the structural columns and floors, Viraspan™ factory-applied, fire-fused ceramic frit paint was applied in high-opacity white and in medium gray.
Further contributing to project’s green goals, the ClearStory™ sun shade blades are engineered as an integral part of the curtainwall systems. Sun shades provide shading from direct sunlight, glare protection and daylight redirection, and help to reduce HVAC peak loads with corresponding reductions in mechanical equipment capacity and carbon footprint.
“These are not your traditional, horizontal sun shades,” notes Batten. “Rather, these are custom, 9-inch-deep, vertically installed, angular covers. They are key elements in the building’s aesthetic on the South and West elevations.”
To ensure the proper integration of sun shades and curtainwall, Wausau developed 3-D printed “rapid prototypes” from CAD data. “The opposite of traditional, subtractive manufacturing, which produces objects by cutting material away, 3-D printing is an additive process, where the printer extrudes and deposits molten thermoplastic in layers to build the part from the bottom up,” explains Wausau’s educational market manager, Steve Gille.
3-D printing is “big advantage that Wausau can offer,” says Batten. “The 3-D printing was extremely helpful as the project has many custom profiles. Typically, these are seen and approved using 2-D shop drawings. Utilizing 3-D printing allowed Wausau to print a visual sample showing the new profiles along with the existing profiles. This allowed the architect, owner and construction manager to see what the final assembly will look like before any material was actually produced.”
Once approved, Wausau began the manufacturing process using recycled aluminum. Supporting the project’s sustainability goals, the curtainwalls’ aluminum framing and sun shade blades contain recycled content averaging 70% or greater. These are fabricated in Wausau’s LEED-Silver certified manufacturing center to ensure the desired performance, and are backed with a standard limited warranty of up to 10 years.
Contributing to the systems’ durability, Linetec is finishing all of the aluminum framing and sun shades in a PPG Duranar® Sunstorm™ Silver three-coat paint. As a 70% polyvinylidene fluoride (PVDF) resin-based coating, this finish meets American Architectural Manufacturers Association’s AAMA-2605 — the most stringent, exterior, architectural specification. PVDF finishes exhibit outstanding resistance to humidity, color change, chalk, gloss loss and chemicals.
As an environmentally conscious finisher, Linetec safely captures and destroys the VOCs present in liquid solvent-based paints at the factory before arrival on the building site. Wausau’s finished products comply with indoor environmental quality credits for low-emitting materials with respect to LEED criteria.
The silver colored, aluminum and glass curtainwall maintains the architectural vernacular of the surrounding buildings, complemented by the granite stone veneer that will clad 3737 Market Street’s ground floor. Familiar with the neighborhood’s aesthetic and the development, ZGF and UJMN have partnered on several projects in Philadelphia’s University City district.
At 180,000 people, Philadelphia has the third largest residential population among Central Business Districts in the U.S. The area is flush with academic researchers, healthcare institutions and life science and technology companies. According to the Science Center’s 2013 annual review, $9.4 billion in annual regional economic output is generated by its graduate and resident organizations. Eight thousand people work on the Science Center’s campus every day and the 93 graduate companies that are located in the greater Philadelphia region employ 15,000 people.
The new 3737 Market Street tower will be the 15th building in the research park and part of its more than 2 million square feet of laboratory and office space. The new construction also marks a dramatic expansion of Penn Presbyterian Medical Center (PPMC), adding more than 150,000 square feet of state-of-the-art outpatient surgery, treatment and rehabilitation facilities, including nearly 110 exam rooms, six outpatient operating rooms and an outpatient radiology center. Good Shepherd Penn Partners will occupy an additional floor and a half in the building. A restaurant and shops will lease approximately 6,000 square feet of retail space on the ground floor.
The Science Center and Wexford Science + Technology will control the remaining square footage in the building for other uses related to the Science Center’s mission of supporting tech-based innovation, entrepreneurship and economic development in the region. Along with emboldening the Science Center’s mission and pursuing LEED Silver certification, 3737 Market Street addresses additional community-driven aspirations.
The University City district has a Sustainability Steering Committee to coordinate efforts guided by Mayor Michael A. Nutter’s Greenworks Philadelphia agenda to become the greenest city in America. These goals include:
* Assisting businesses with energy efficiency improvements that reduce consumption and save money;
* Hosting workshops for businesses and residents, and providing training for local youth and adults;
* Increasing recycling, composting the leaves that are collected each fall, and making compost and mulch available to community gardens;
* Sponsoring a new Farmers Market and promoting access to local healthy food;
* Improving use of area parks, including more than 33,000 square feet of concrete repurposed for social spaces;
* Promoting transit use and making University City more walkable by installing new pedestrian lights and bump-outs; and
* Creating green streets by constructing rain gardens, greening traffic islands, planting trees and installing sidewalk planters.
The Science Center also has partnered with the City of Philadelphia’s “ReStore Philadelphia Corridors” program, and with neighboring landlords and property owners to revitalize the Market Street streetscape, enhance its infrastructure and increase safety.
“Our mission is to create a community of innovators and entrepreneurs,” said Stephen S. Tang, Ph.D., MBA, the Science Center’s president and CEO. “Over time the shape of those innovation communities has changed. They are no longer just places to work.”
He added, “Penn Presbyterian’s expansion onto the Science Center campus strengthens University City’s unparalleled reputation as an Eds and Meds hub. We are delighted that we’ll be celebrating the Science Center’s 50th anniversary in 2013 with construction cranes on our campus. It sends a positive message about the economic recovery, job creation and the desirability of University City as an innovation center.”
“This expansion will provide PPMC faculty and staff with the infrastructure necessary to better serve the Powelton Avenue, West Philadelphia, and even the Greater Philadelphia communities,” noted Michele Volpe, CEO of Penn Presbyterian Medical Center. “Since PPMC was founded in 1871, it has proved to be a leader in providing top-quality patient care. Our new building will only further reinforce our commitments to excellence, our patients and our community.”
“We are very excited to continue our partnership with the Science Center with the development of 3737 Market,” echoed James R. Berens, chairman of Wexford Science + Technology. “The project, as a mix of clinical, research and office uses, is a perfect match to the Science Center’s mission and Wexford’s capabilities — and is a great opportunity to cultivate University City and Philadelphia’s innovation cluster.”
At the Association of University Research Parks’ awards ceremony in September 2013, Wexford Science + Technology was presented with a “Leadership Award” for its “outstanding contribution to the success and total community impact of multiple university research and technology parks.” The University City Science Center also was honored as the 2013 “Developing the Culture of Innovation Award” for “50 years helping entrepreneurs to invent the future by providing both the physical space and the key resources needed to help commercialize new technologies throughout the Greater Philadelphia region.”
**
University City Science Center, 3737 Market St., Philadelphia
* Owner – joint venture: University City Science Center; Philadelphia; https://www.sciencecenter.org
and Wexford Science + Technology; Baltimore; http://wexfordscitech.com
* Architect: Zimmer Gunsul Frasca (ZGF) Architects; https://www.zgf.com/
* Associate architect: UJMN Architects + Designers; Philadelphia; http://www.ujmn.com
* General contractor: INTECH Construction; Philadelphia; http://www.intechconstruction.com
* Glazing contractor: R.A. Kennedy and Sons, Inc.; Aston, Pa.
* Glazing systems – manufacturer: Wausau Window and Wall Systems, 7250i-UW Series thermal unitized curtainwall, 10250 Series structural silicone glazed curtainwall, ClearStory sun shades; Wausau, Wis.; http://www.wausauwindow.com
* Glazing systems – glass: Viracon; Owatonna, Minn.; http://www.viracon.com
* Glazing systems – finisher: Linetec, Wausau, Wis.; http://www.linetec.com
* Photographer: Mark Long
###
Filed under: AAMA, AIA, Buildings + Infrastructure, CLIENT NEWS, Green Goals, Linetec, Projects, Tradeshow Thoughts, USGBC, Wausau Window and Wall Systems | Comments Off on Client News: University City Science Center expands “Eds and Meds hub,” features Wausau’s INvision curtainwall and ClearStory sun shades